Dreischienige Gleisjoche umarbeiten
[ vorherige Seite | Homepage
]
Da es inzwischen schwer geworden ist, altbrauchbare meterspurige
Holzschwellen zu bekommen, und Regelspurschwellen umarbeiten wegen der
notwendigen Ausfräsung der Auflagerflächen für die
Rippenplatten sehr aufwändig ist, haben wir die Gelegenheit genutzt,
dreischienige Schwellen der Stuttgarter Straßenbahn, die in einem
mittlerweile aufgegeben Stadtbahntunnel lagen, zu erwerben.
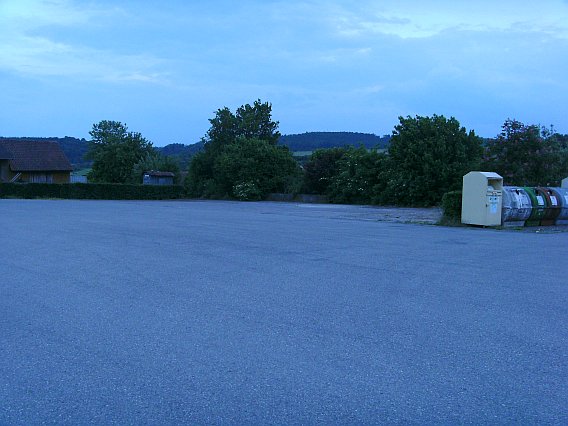 |
Zuvor mussten wir einen freien Platz zum
zwischenlagern der Gleisjoche schaffen.
Hier bot sich die Fläche des ehemaligen Recyclinghofs an, die uns
bisher zum Teil als Schwellenlagerplatz diente. |
Die Schwellen haben vorläufig einen neuen Platz
gefunden, bis wir eine Transportmöglichkeit auf die Strecke haben. |
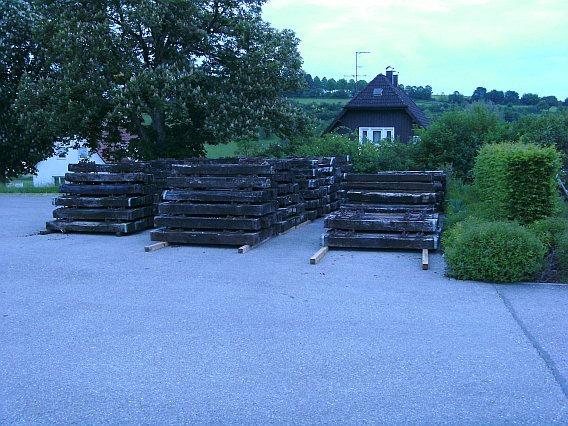 |
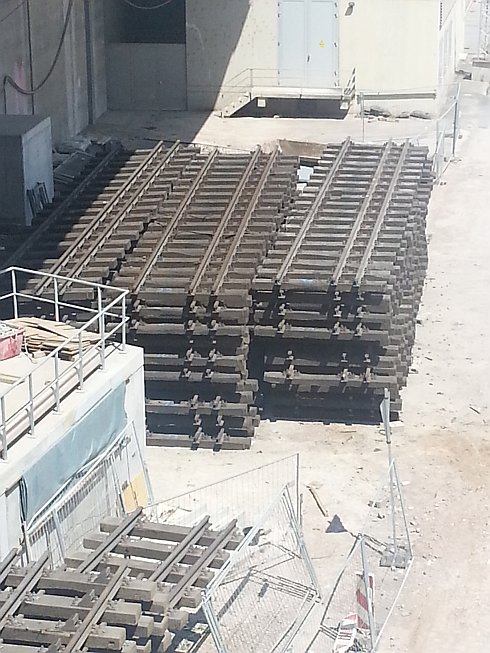 |
Jetzt sind wir in Stuttgart, hier werden die
Gleisjoche aus dem Tunnel heraus transportiert und zwischengelagert.
In der Regel sind die Joche auf 12 Meter geschnitten. |
Bei den Umbauarbeiten sind auch auch kürzere Stücke
angefallen. Hier werden wir die Schienen nicht mehr als Fahrschienen
verwenden, aber als Zaunpfosten und für den Bahnsteigbau sind die
kurzen Stücke immer noch brauchbar. |
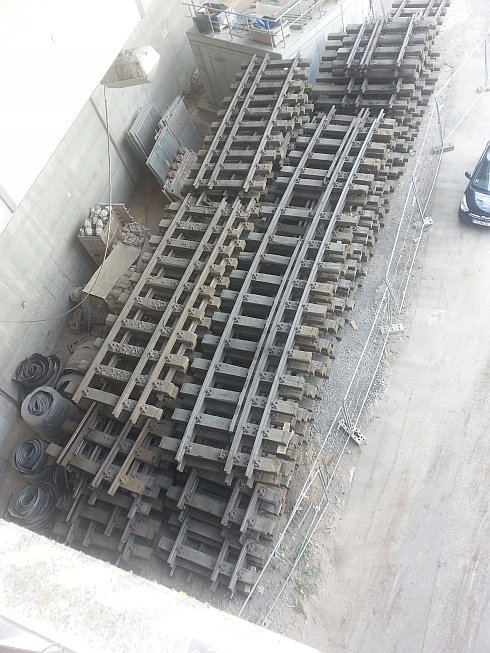 |
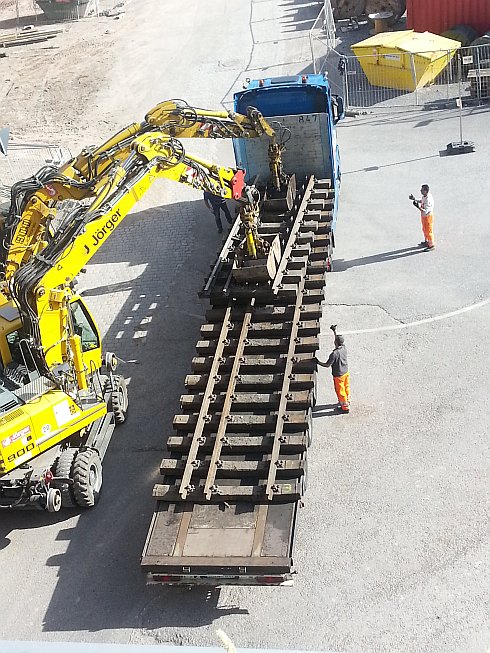 |
Dann wurden die Joche verladen.... |
.... nach Neresheim gebracht und auf dem Lagerplatz
aufgestapelt.
Bei dieser Menge handelt es sich ca. um die Hälfte der gesamten
Menge, die wir bekommen. |
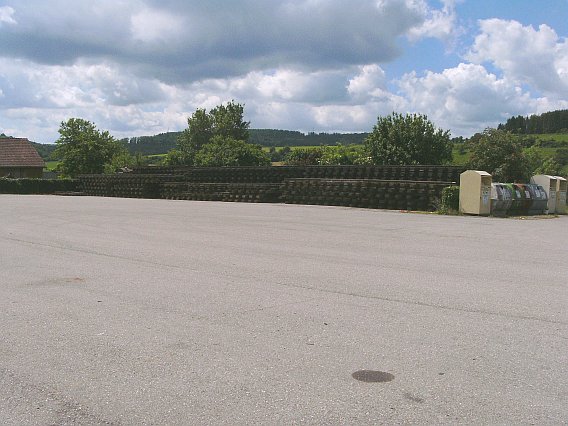 |
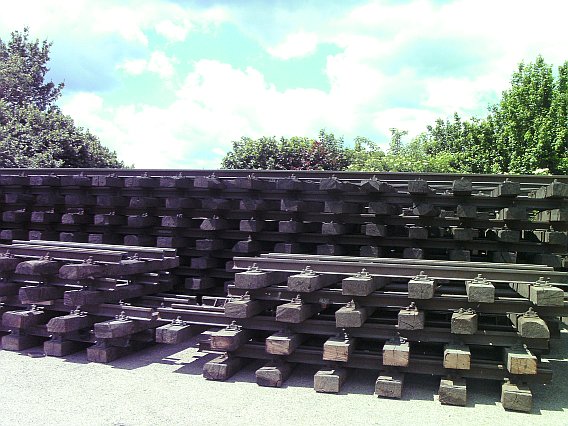 |
Es sieht hier aus wie bei der Modelleisenbahn, 1/1
Schienen im Hintergrund |
hier 1/2 Schienen |
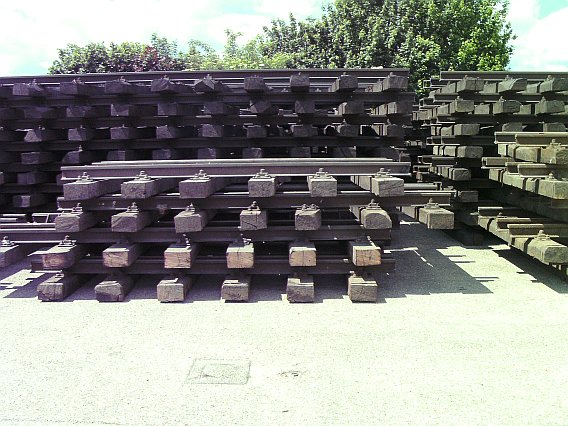 |
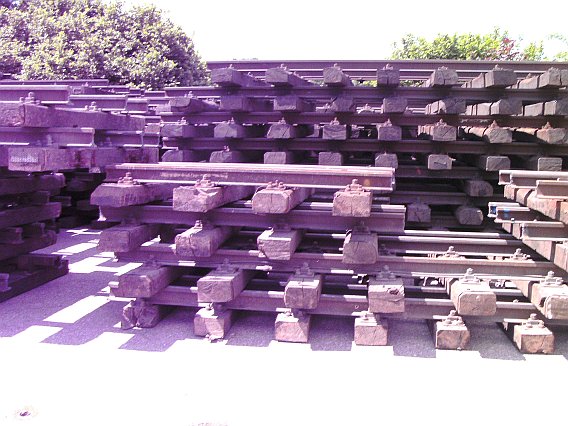 |
und hier 1/4 Schienen |
Zum Teil sind auch noch Schutzschienen aus engen Bögen
montiert. |
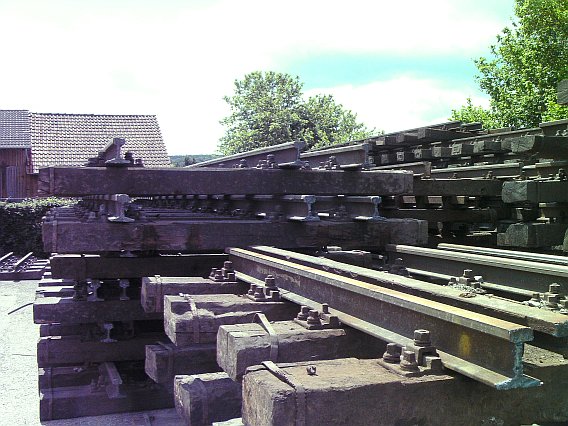 |
Über das Zerlegen der Joche und Umarbeiten der Schwellen werde ich
zu gegebener Zeit berichten.
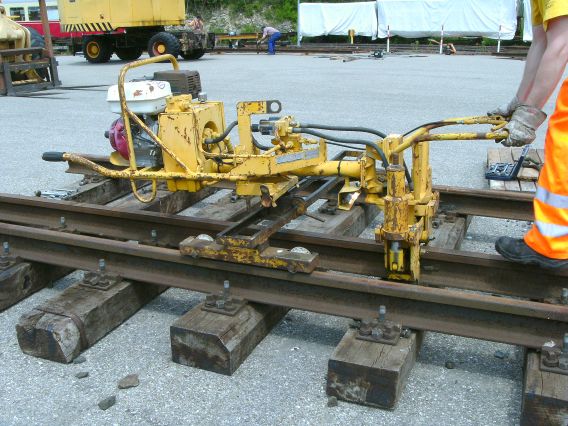 |
Hinter diesem Wortmonster verbirgt sich eine große
Arbeitserleichterung.
Mussten bisher die Hakenschrauben nach dem Entfernen der Schiene,
worunter oft die Gewinde litten, mit Hammer und Durchlag mühsam
einzeln aus der Rippenplatte geklopft werden, erledigt das nun diese
Maschine. |
Nach dem Lösen der Schrauben mit der
Schraubmaschine und dem Entfernen der Klemmplatten kommt die
Hakenschraubenausdrückmaschine zum Einsatz. |
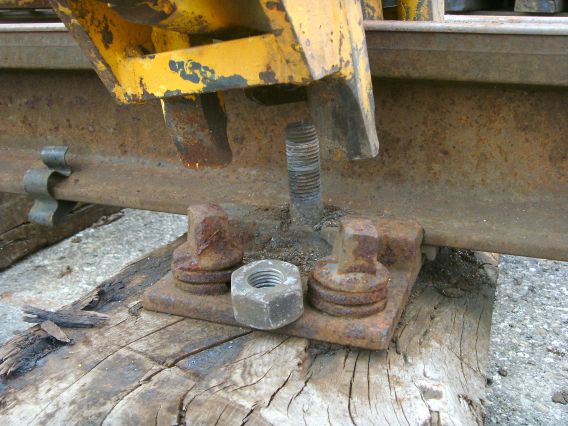 |
 |
Auf die Rippenplatte aufgesetzt greifen die halbrunden
Ausdrückhebel die Schraube direkt über der Rippe an und werden
hydraulisch nach aussen geschwenkt. |
Mit einem vernehmlichen 'knock' wird die meist durch
Bremssand und Rost festsitzende Schraube aus dem Schwalbenschwanz der
Rippenplatte gedrückt. |
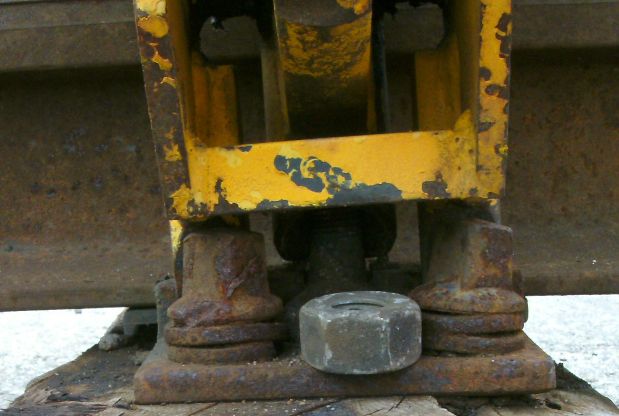 |
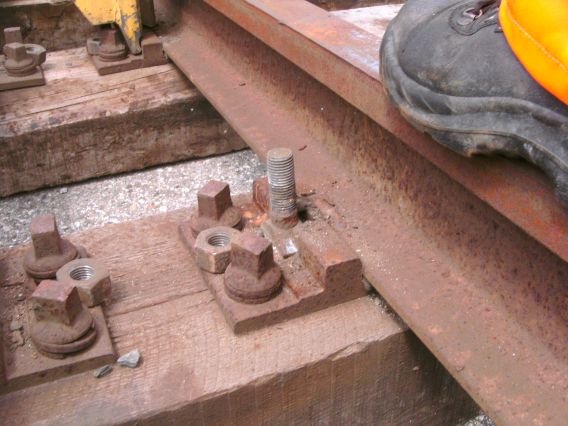 |
Und im Gegensatz zum Austreiben mit dem Hammer fliegt
sie nicht weg, sondern bleibt brav stehen und kann wieder mit ihrer
Mutter vereint eingelagert werden. |
Die Geschwindigkeit, mit der diese Maschine die Schrauben ausdrückt,
ist beeindruckend, alle 10 Sekunden ertönt das 'knock', das anzeigt,
daß wieder zwei Schrauben gelöst sind.
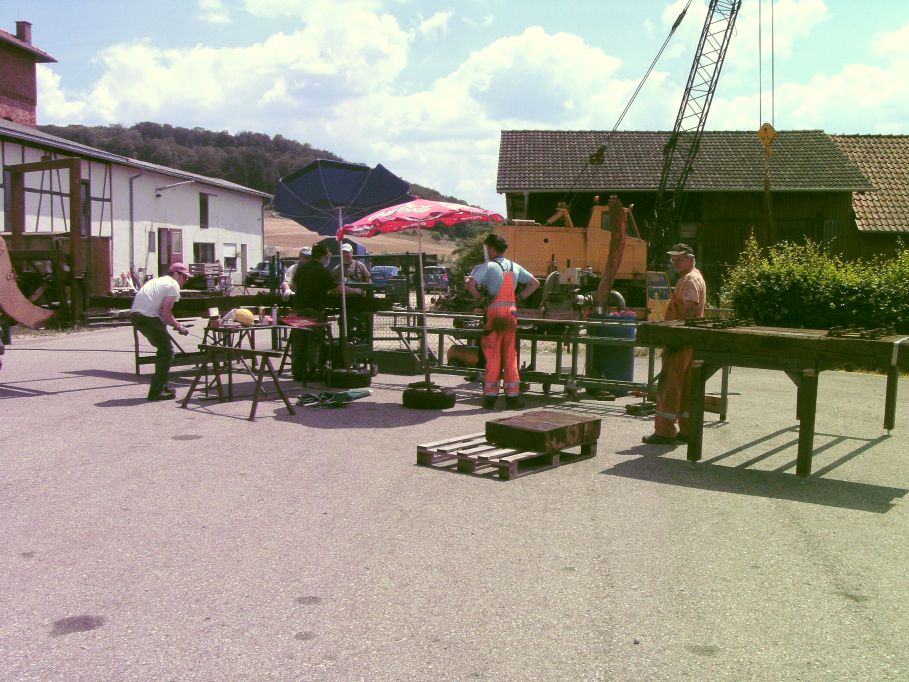 |
Um die Regelspurschwellen nach dem entfernen der
dritten Rippenplatte auf die richtige Länge zu bringen, muss ca.
ein halber Meter der Schwelle abgesägt werden. Und da wir im Laufe
der Zeit ca. 2000 Schwellen zu sägen haben, haben wir uns eine Art
Fertigungsstrasse aufgebaut.
Links werden die Schwellen mit dem Radlader angefahren, danach werden
sie bandagiert, gesägt, verpflockt und rechts dann wieder vom
Radlader abgeholt. |
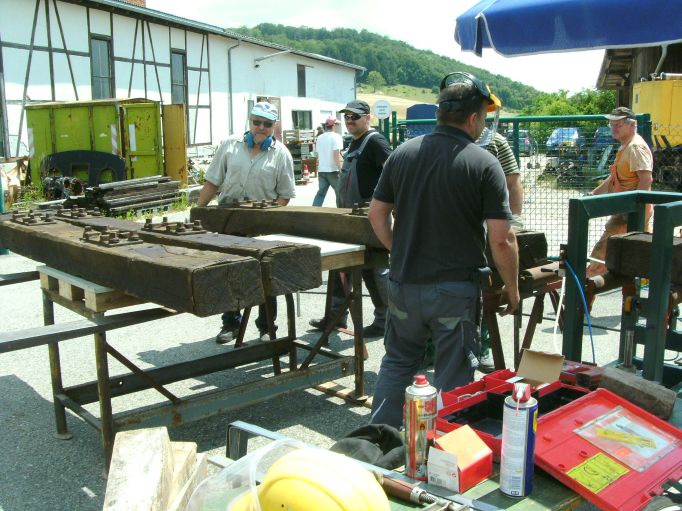 |
Auf diesem Tisch, dessen Oberfläche mit Blech
beschlagen ist, werden immer 5 Schwellen abgelegt und dann auf eine
Rollenbahn gezogen. |
Über die Rollenbahn werden die Schwellen dann in
unsere selbstgebaute Bandagiermaschine geschoben, um das Aufreissen der
Schwelle nach dem Sägen zu verhindern.
Der Druckluftzylinder unten spannt das Band, abhängig vom
eingestellten Luftdruck, mit bis zu 2 Tonnen Zug. |
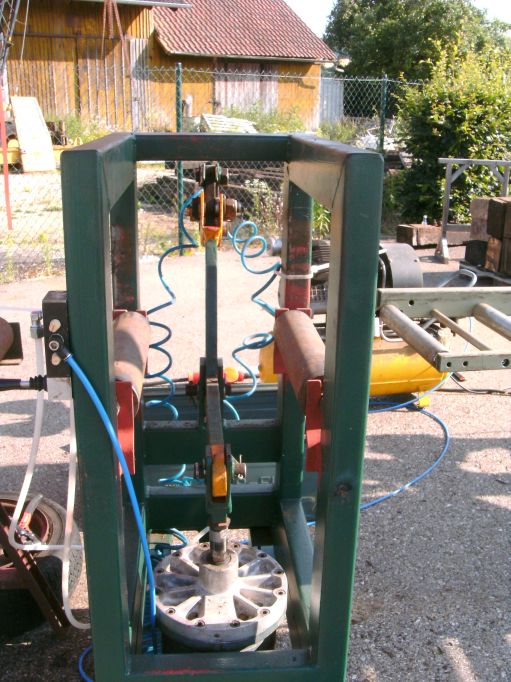 |
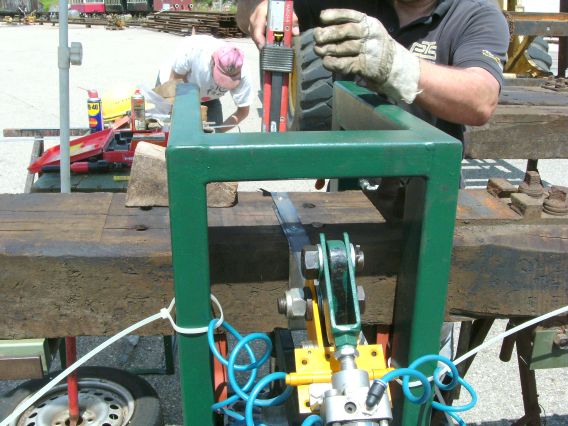 |
Ein Metallband wird an der Schwelle festgenagelt,
herumgeschlungen und mit der Spannvorrichtung gespannt.
Dann werden zwei weitere Nägel durch die überlappten
Bandlagen in die Schwelle geschossen. |
Das überstehende Ende des Bandes wird abgeschert. |
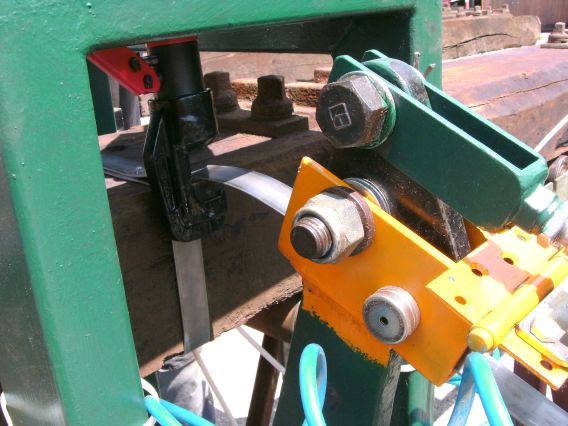 |
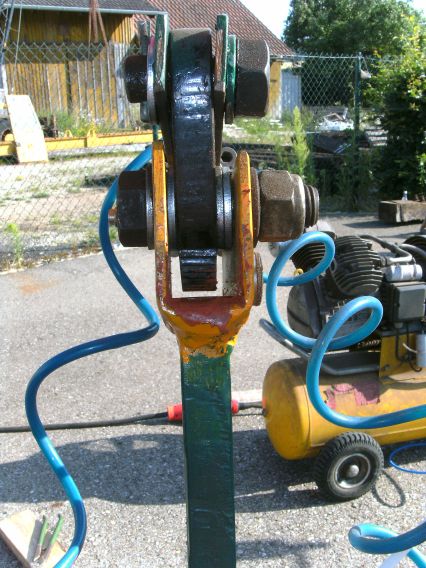 |
Die Spannvorrichtung im Detail, hier ist sie geöffnet
und das Band kann eingeschoben werden. |
Geschlossen ziehen sich die Krallen durch den Zug in
das Band.
Das Öffnen und Schließen der Spannvorrichtung geschiet per
Druckluft und wird über einen Fusstaster gesteuert, damit man die Hände
frei hat. |
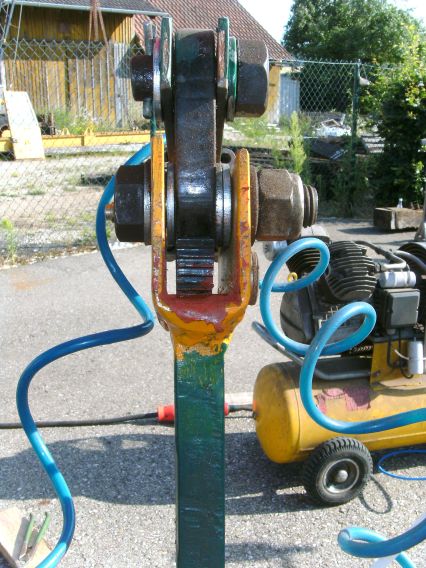 |
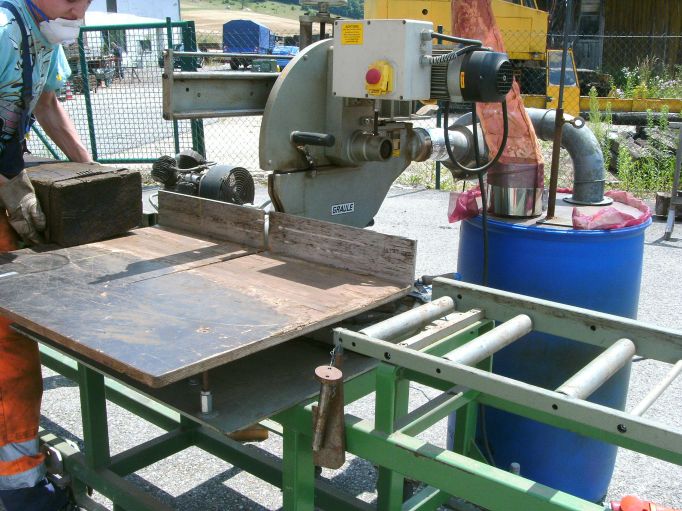 |
Nach dem bandagieren rückt die Schwelle über
eine weitere Rollenbahn zur Säge vor |
Die Säge frisst sich in relativ schnell durch das
harte Eichenholz, im Hintergrund wird bereits die nächste Schwelle
bandagiert. |
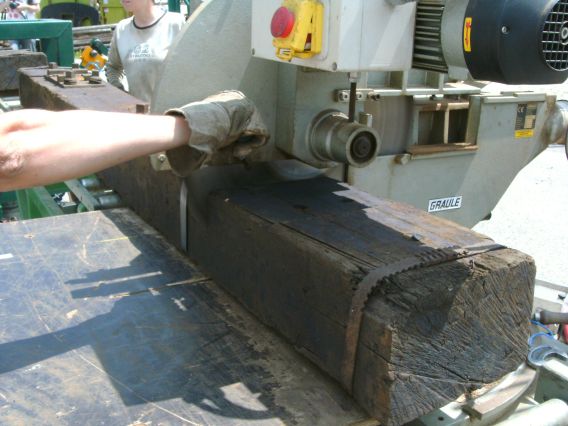 |
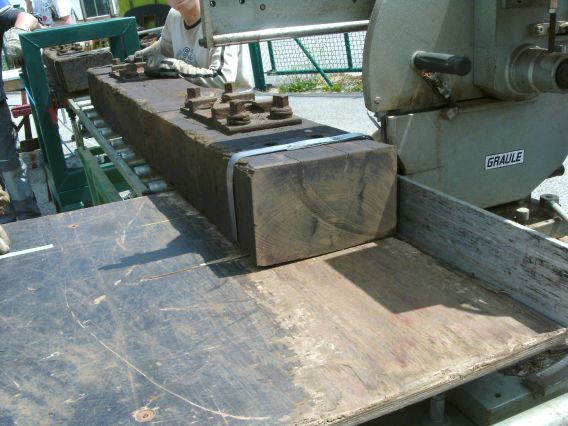 |
Jetzt hat das neue Band die Aufgabe, die Schwelle vor
dem Aufreissen zu schützen, übernommen. |
Das abgesägten Stücke werden bis zur
Entsorgung auf eine Palette gestapelt. |
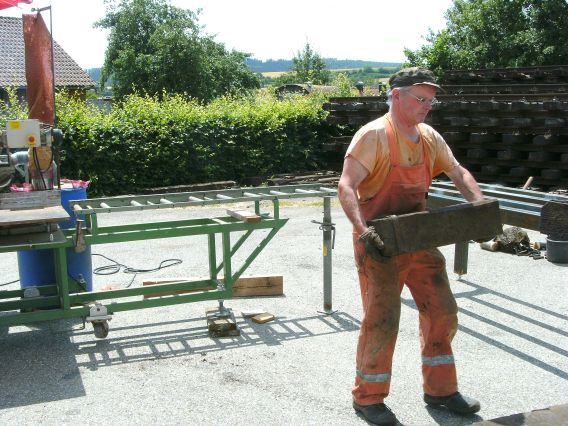 |
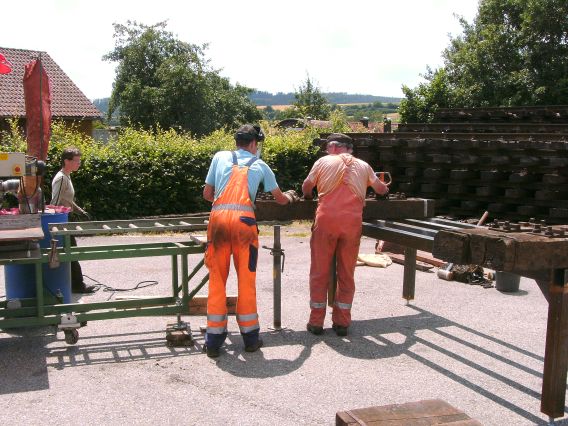 |
Die Schwelle selbst wird über die Rollenbahn auf
einen weiteren Tisch verbracht... |
... wo die zwei verbliebenen Löcher der dritten
Schienenbefestigung verpflockt werden... |
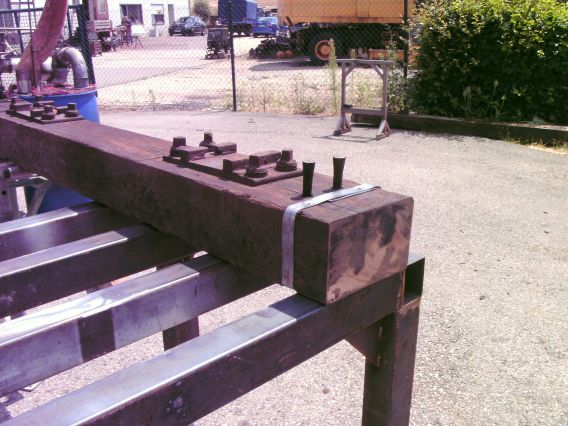 |
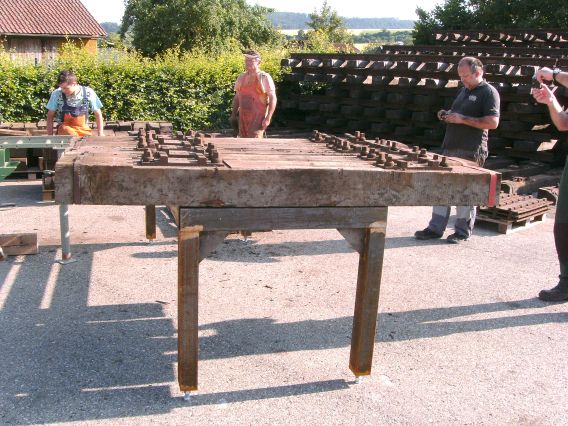 |
...bevor die Schwellen für den Abtransport ans
Ende des Tisches geschoben werden. |
Das beim Sägen anfallende Sägemehl wird
abgesaugt und in die Tonne geblasen, wo es zur fachgerechten Entsorgung
gesammelt wird. |
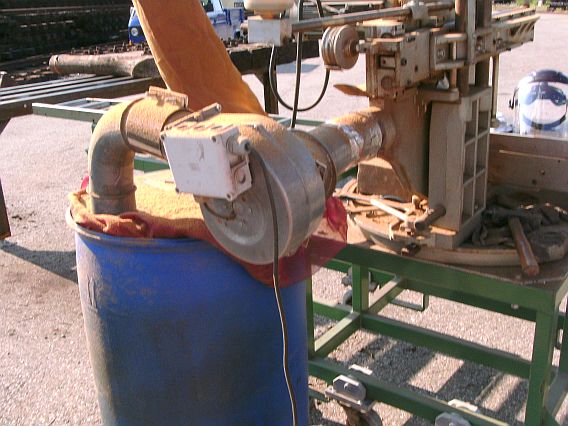 |
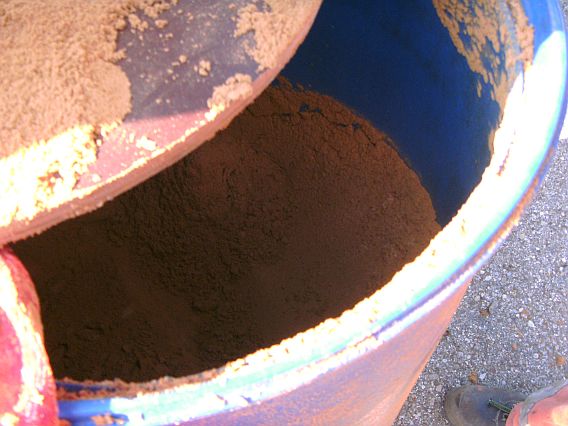 |
Nach einem Tag Sägen kommen über 100 Liter Sägemehl
zusammen. |
Bei dieser ersten Sägeaktion, bei der wir erst einmal die
Arbeitsabläufe ausprobieren und optimieren mussten, konnten wir 95
Schwellen sägen. Jetzt, wo wir wissen, wie wir aufzubauen haben und
vielleicht noch die eine oder andere Optimierung einbauen können,
gehen wir davon aus, bis zu 200 Schwellen am Tag sägen zu können.
[ vorherige Seite | Homepage
]
Copyright © 2017 - 2018, Gerald Stempel,
Gerald.Stempel@t-online.de
[ Letzte Aktualisierung 15.07.2018 Gerald Stempel ]