Der Gleisbau - Schwellenaufarbeitung
vorherige Seite
Die Problematik
hatten wir im ersten Bauabschnitt überwiegend bereits fertig
aufgeplattete Schwellen zur Verfügung, die mehr oder weniger ohne große
Vorarbeiten wieder eingebaut werden konnten, haben wir jetzt das Problem,
auf unbeplattetet Schwellen, Schwellen mit nicht passender Spurweite oder
sogar auf Regelspurschwellen bzw. Schwellen aus dreischienigen Abschnitten
zurückgreifen zu müssen.
Schwellen sortieren
Die Schwellen, ob beplattet oder unbeplattet, müssen anhand der
vorhandenen Lochabstände bzw. der Abstände der Rippenplatten
sortiert werden. Welche Spurweiten sich aus den Ist-Maßen ergeben,
haben wir rechnerisch und experimentell ermittelt. Ziel ist, in den
Geraden auf eine Spurweite zwischen 995 mm (unteres Grenzmaß)
und 1005 mm zu kommen. Für Bögen je nach Radius 1000 mm
bis maximal 1025 mm (oberes Grenzmaß).
Alle Schwellen, die unter oder über diesen Maßen liegen, müssen
verdübelt und neu gebohrt werden. Manche der Schwellen würden
ohne entsprechende Maßnahmen eine Spurweite von 980 mm!!
ergeben.
Schwellen aufarbeiten (bandagieren, Eisen einschlagen, verdübeln)
Normalerweise sind die Schwellenenden mit Stahlbändern oder
eingeschlagenen Klammern gegen das Aufspalten beim Eindrehen der Schrauben
gesichert. Bei gebrauchten Schwellen sind diese Sicherungen oft stark
korrodiert und gerissen. Solange die Schwellenschrauben nicht entfernt
werden, passiert in der Regel nichts, bei den unbeplatteten Schwellen
besteht jedoch die Gefahr, daß sie beim Aufplatten reissen. Hier müssen
wir die Schwellenenden sichern.
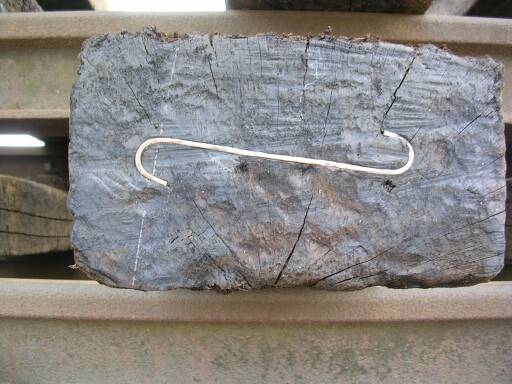 |
Bei gut erhaltenen Schwellen werden S-Haken
eingeschlagen, die das auseinanderreißen der Schwelle verhindern,
wenn die Schrauben eingedreht werden. |
Arbeitsgänge zum Bandagieren einer Schwelle
Bei bereits eingerissenen Schwellen wird
das Schwellenende mit einem Stahlband umspannt, um das weitere Reißen
zu verhindern. Der vorhandene Riß muß möglicht fest
zusammengepresst werden. Dazu wurde Anfangs ein selbstgebauter
Kettenspanner verwendet, der folgendermaßen funktionierte: |
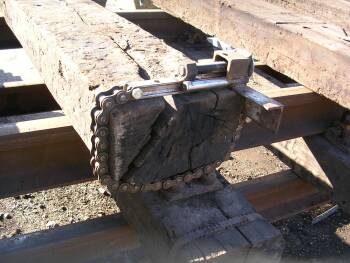 |
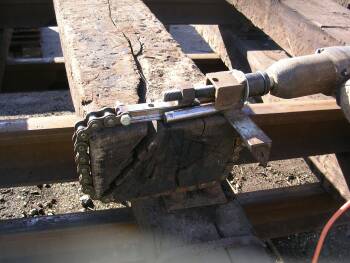 |
Der Kettenspanner wurde um das gerissene Ende gelegt
und die Gewindespindel
|
mit einem Schlagschrauber angezogen.
Bei Regenwetter, wenn aus Sicherheitsgründen keine Elektrogeräte
im Freien eingesetzt werden können, geht das auch mit dem
Schraubenschlüssel.
|
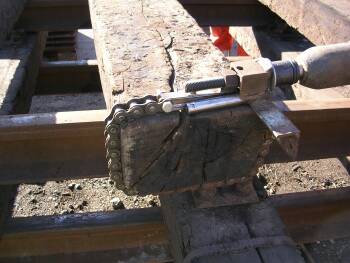 |
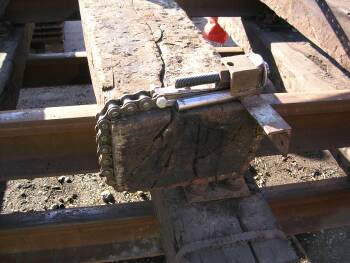 |
Langsam zieht sich der Spalt zu....
|
... bis er fest zusammengepresst ist.
|
|
|
Nun wird das Band um die Schwelle gelegt, ...
|
... um die Kanten gehämmert, daß es möglicht
fest anliegt...
|
|
|
... und mit Nägeln gesichert. Nach dem Abnehmen
des Kettenspanners hält das Band die Schwelle zusammen.
|
So sieht das Ergebnis dann aus.
|
Leider hat es sich gezeigt, daß die Gewindespindel des oben
gezeigten Kettenspanners auch bei bester Schmierung keine lange
Lebensdauer hat und sehr schnell verschleißt. Der Grund dürfte
darin zu finden sein, daß der Druck zum zusammenpressen der Schwelle
nach unseren Berechnungen bei zwei bis vier Tonnen liegen dürfte.
Deshalb haben wir einen neuen Schwellenspanner gebaut, der hydraulisch
arbeitet und nach inzwischen weit über 200 Spannvorgängen noch
keinerlei Verschleißerscheinungen zeigt.
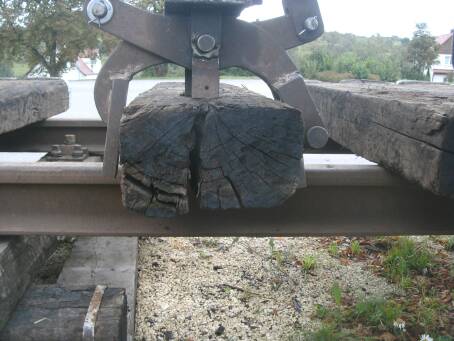 |
Die hydraulische Presse wird auf die Schwelle
aufgesetzt.... |
.... und die Backen pressen die Schwelle zusammen .... |
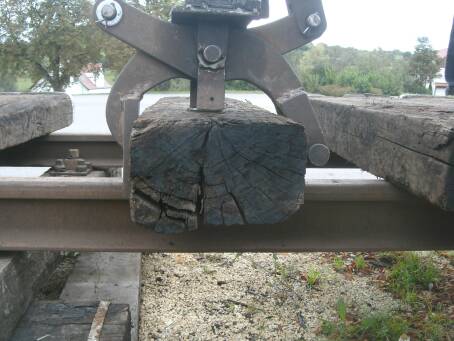 |
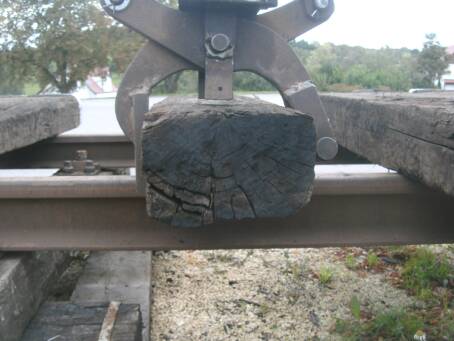 |
.... bis der Spalt zusammengepresst ist.
Dann wird das Band wie gehabt um die Schwelle gehämmert und
vernagelt. |
Und so funktioniert unsere hydraulische
Schwellenpresse. Die geöffnete Schere wird auf die Schwelle
gestellt und mit einem handelsüblichen Hydraulikwagenheber über
die Zugstangen geschlossen. Der Druck dieser Presse kann unseren
Berechnungen nach bis zu ca. 5 Tonnen betragen. |
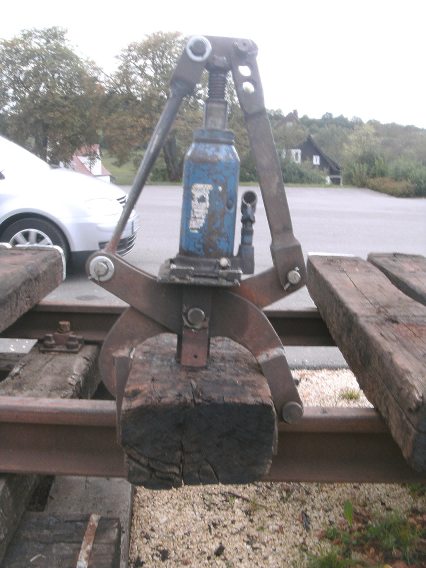 |
Der Vorteil dieser Presse ist, daß sie bisher keinerlei Verschleißerscheinungen
zeigt und auch keinen Strom benötigt. Der Kraftaufwand beim Pumpen hält
sich in Grenzen, dafür hat die ganze Mechanik ein ziemliches Gewicht.
Da sich der Wagenheber aber leicht herausnehmen lässt, er steht nur
lose zwischen Führungsleisten, ist das auch kein Problem.
Verdübeln überflüssiger Bohrlöcher
Zum Teil sind in den Schwellen Löcher, die wir
nicht benötigen. Diese vier Löcher stammen von der Befestigung
einer Schutzschiene. Wir bauen keine Schutzschiene ein und müssen
die Löcher deshalb gegen eindringendes Wasser verschliessen.
Sand und Schmutz werden ausgekratzt..... |
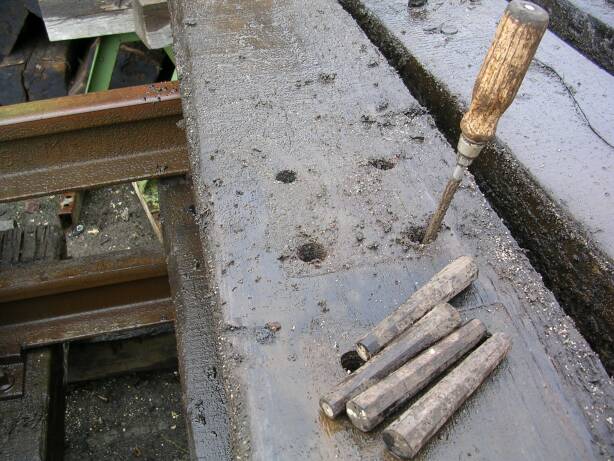 |
 |
... dann werden Holzdübel in die Löcher
gesteckt und eingeschlagen. Durch die Keilform werden die Löcher
dicht verschlossen. |
So sieht dann das Ergebnis aus. |
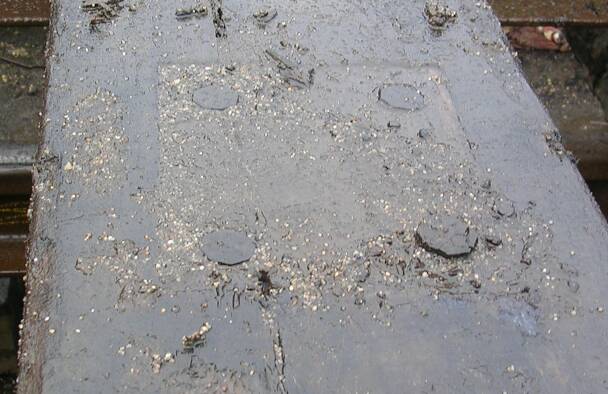 |
Ein großer Teil der Schwellen, die wir auf Lager haben, ist von
den Lochabständen der Bohrungen etwas zu eng und muß neu
gebohrt werden. Bei aufgeplatteten Schwellen werden dazu zuerst die
Platten entfernt, die Löcher auf einer Seite verdübelt und die
Schwellen mit unserer Bohrlehre neu gebohrt.
Bohrlöcher reinigen
Eine mühsame, aber notwendige Arbeit bei den unbeplatteten
Schwellen ist das sauber machen der Schraubenlöcher, die zum Teil
beim Ausbau, der Zwischenlagerung oder beim Verladen mit Sand, kleinen
Steinen oder Erde gefüllt wurden. In diese Löcher können
weder Schrauben eingedreht noch Dübel eingeschlagen werden. Zuerst muß
der Schmutz raus.
Anfangs wurde er, wie oben zu sehen, mit Schraubendrehern und ähnlichem
ausgekratzt, inzwischen haben wir aber eine bessere Methode gefunden.
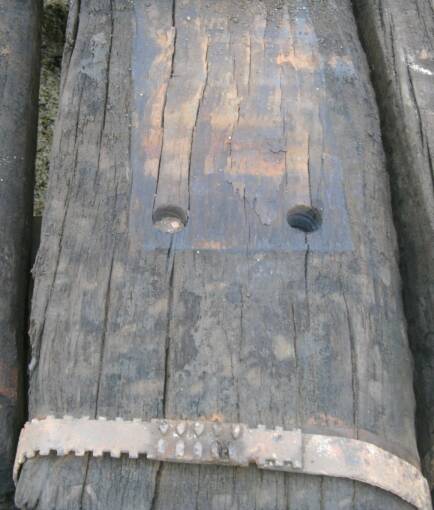 |
Wenn das Bohrloch so zugesetzt ist, muß es
sauber gemacht werden. |
Mit einem Bohrer, wir verwenden dazu einen alten
Schlangenbohrer, wird der Schmutz aufgebrochen und gelöst und mit
einem Ruck herausgerissen, wie am rechten Loch zu sehen ist.
Um den restlichen Schmutz auch noch aus dem Loch zu bringen, werden die
Schwellen umgedreht und mehrfach auf dem Baujoch aufgeschlagen. |
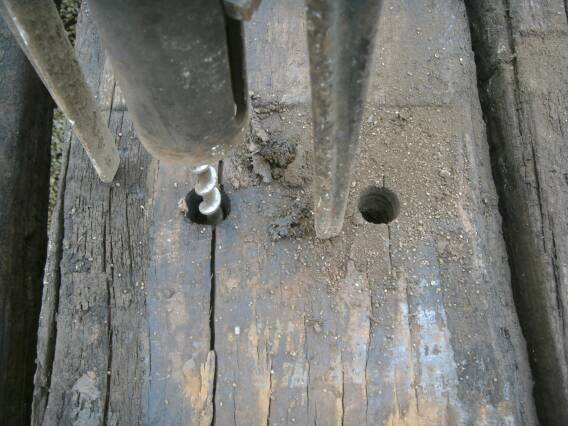 |
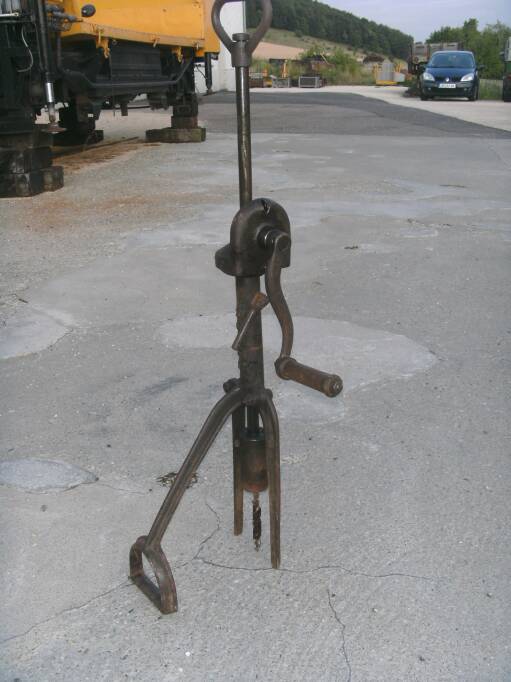 |
Zum Ausbohren nehmen wir dieses Schwellenbohrgerät
mit Handkurbel. Eigentlich ist das ja schon ein Museumsstück, aber
für diese Arbeit ist es unschlagbar. Man bohrt mit viel mehr Gefühl
als mit einer elektrischen Bohrmaschine, diese könnte die Bohrlöcher
aufweiten und die Schrauben würden danach nicht mehr halten.
Vor allem ist die Spindel einfacher heraus zu ziehen, da man nicht die
ganze Maschine hochheben muß. |
Die Maschine hat schon ein stolzes Alter erreicht. |
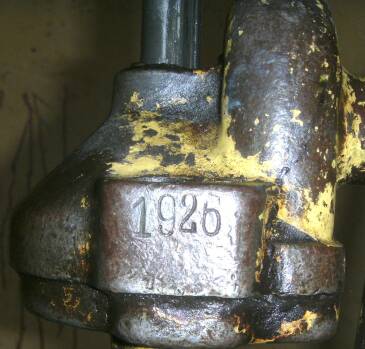 |
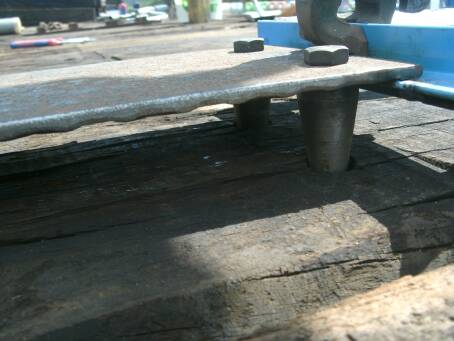 |
Unsere Schwellenbohrschablone besteht aus drei Teilen:
Teil eins ist eine Platte mit vier Zentrierspitzen und einem
Anschlagwinkel. Die Platte wird in die vier vorhandenen Löcher der
Schwelle gesteckt und bietet damit die Referenz zum Bohren der anderen
Seite der Schwelle. |
Am anderen Ende liegt die eigentliche Bohrschablone
mit ihren vier Bohrhülsen. |
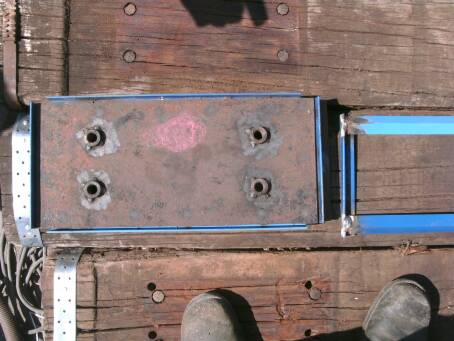 |
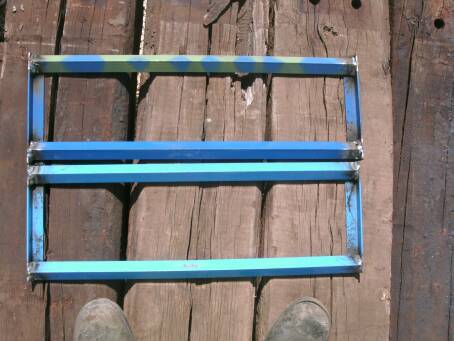 |
Der Abstand zwischen den beiden Teilen wird durch
Zwischenrahmen hergestellt. Wie hier zu sehen ist, haben wir diese
Rahmen in verschiedenen Größen angefertigt (insgesamt 6 Stück),
damit können wir im Raster von 5 mm alle Spurweiten von 1000 mm
bis 1025 mm herstellen. |
Zusammengebaut sieht das so aus. Rechts die Platte mit
den Zentrierspitzen, daran angeklemmt der Distanzrahmen, links die
Bohrschablone mit der Bohrmaschine im Einsatz. |
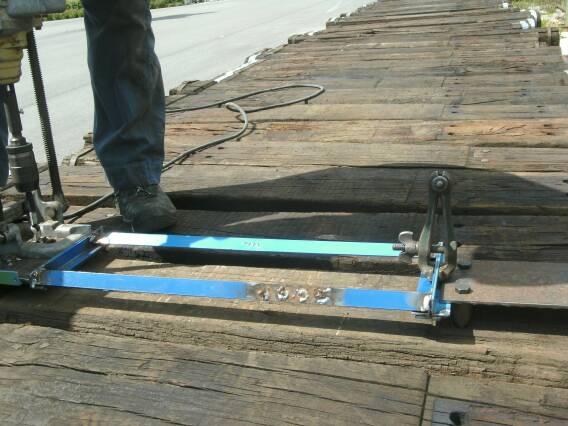 |
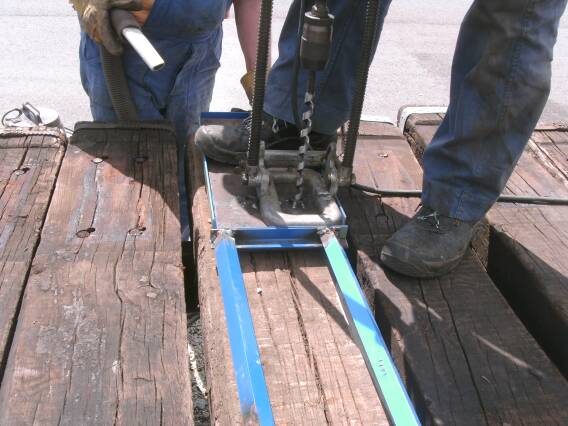 |
Die Bohrschablone ist so konstruiert, daß der
Bohrer genau in die Bohrhülse trifft, wenn der Fuß des Bohrständers
an den beiden Winkeln anliegt.
Mit einem Kesselsauger werden die anfallenden Späne, die ja
schadstoffhaltig sind, abgesaugt, damit sie nicht in die Umwelt
gelangen. |
Das Ergebnis sieht dann so aus. Deutlich zu sehen ist
die Verschiebung der neuen Bohrlöcher von 20 mm gegenüber
den verdübelten Löchern. Die Schwelle ist übrigens für
eine Spurweite von 1005 mm gebohrt. Ohne Korrektur hätte die
Spurweite 985 mm betragen. |
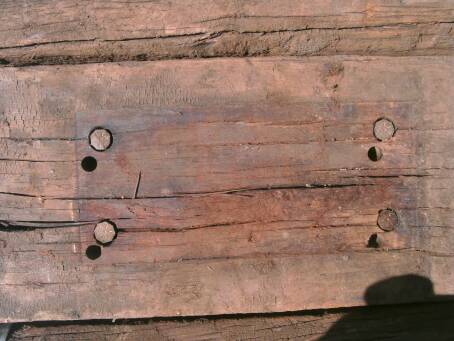 |
Die Konstruktion der Anschlagwinkel erlaubt das parallele, seitliche
Verschieben den Bohrlöcher gegenüber den alten, was die
Spaltbelastung der Schwelle mindert.
Ein kleines Problem besteht noch. Wenn die Bohrerspitze des
Schlangenbohrers beim anbohren etwas verläuft, ist die Reibung des
Bohreres in der Bohrhülse sehr hoch und der Bohrer wird trotz
Schmierung der Hülse heiß. Wir wollen dem begegnen, indem wir
die Bohrhülsen etwas größer bohren.
Ansonsten lässte es sich mit dieser Technik sehr angenehm arbeiten.
Der Bohrer zieht sich fast von selbst in das Holz, solange die Spitze
nicht auf einen Riß trifft, und die Federn des Bohrständers
unterstützen das herausziehen des Bohrers aus dem Bohrloch.
Die Bohrschablone war bisher nur für unbeplattete Schwellen im
Einsatz, wir haben aber auch jede Menge bereits mit Rippenplatten
versehene Schwellen, die die falsche Spurweite haben.
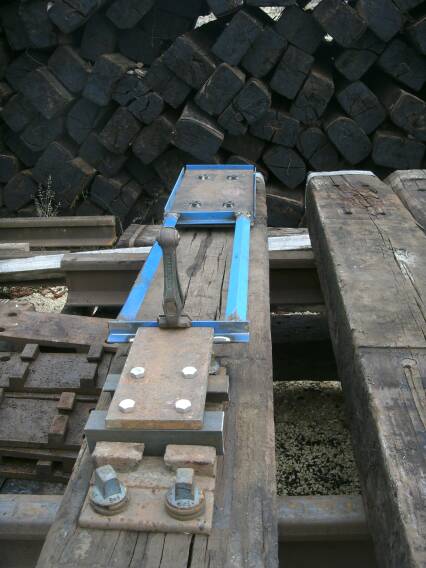 |
Um dort nur eine Platte zu versetzen braucht es eine
Bohrschablone, die sich an der verbleibenden Rippenplatte orientiert. |
Dazu wird der Anschlag mit den Zentrierspitzen einfach
gegen diesen hier ausgetauscht und die Bohrschablone funktioniert genau
so. |
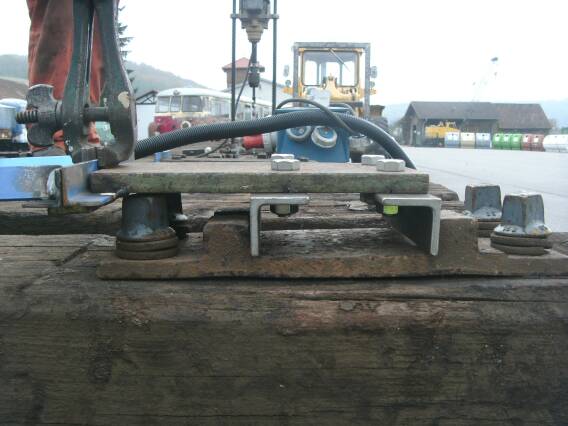 |
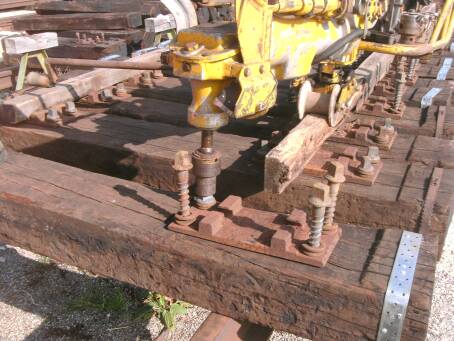 |
Nach dem Auflegen der Rippenplatten und dem Ansetzen
der Schwellenschrauben kommt der Motorschrauber zum Einsatz.
Anstatt auf schweren Schienen, die mit dem Kran eingelegt werden müßten,
nehmen wir Kanthölzer als 'Schienen', das geht genau so gut,
erfordert aber weder den Einsatz eines Krans, noch müssen die
Schwellen exakt ausgerichtet sein, Abweichungen von 4...5cm sind keine
Problem. |
Nur noch wenige Schrauben, dann sind wieder 80
Schwellen fertig für den Einbau. |
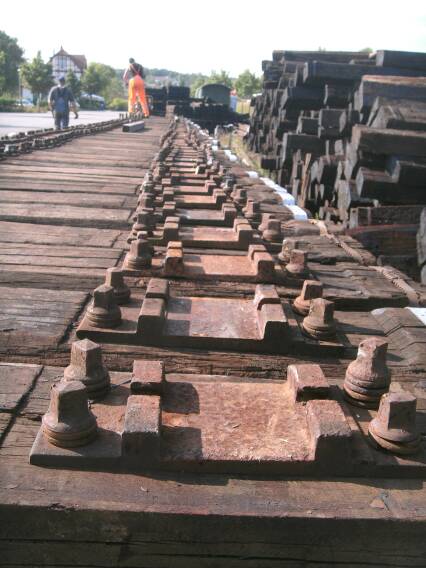 |
Um die Schwellen nicht wie früher mühsam von Hand auf die
Gabeln wuchten zu müssen haben wir uns einen Schwellentransportrahmen
gebaut. Er funktioniert zwar nur bei aufgeplatteten Schwellen, aber die
sind ja auch die schwersten. Bis zu 100 kg können die wiegen.
Der Rahmen kann längs und quer eingesetzt werden und trägt bis
zu zehn Schwellen.
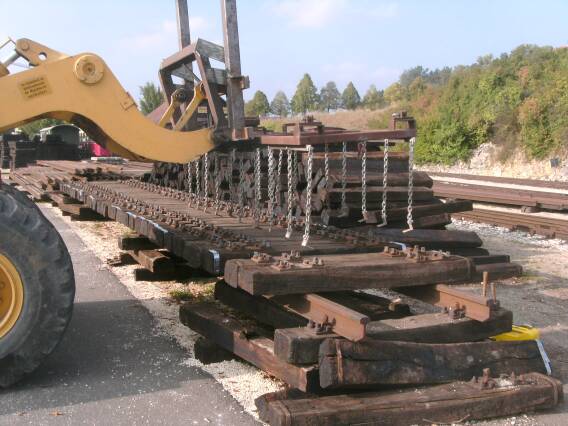 |
Um das Baujoch abzuräumen wird der Rahmen quer
genommen.
Über die Schwellen positionieren... |
.... ablassen, und die Schwellen können angehängt
werden. |
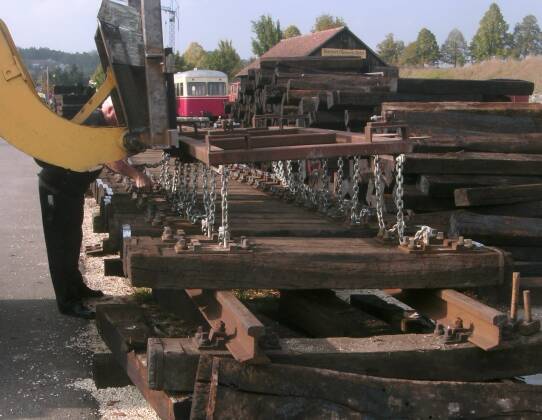 |
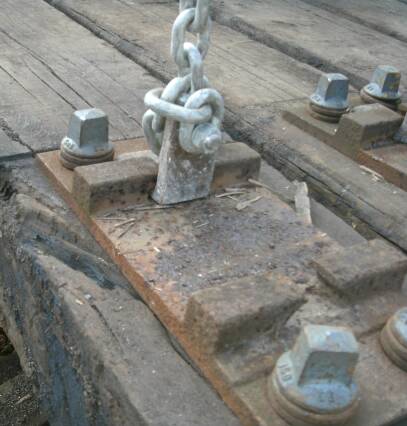 |
Und so hängt die Schwelle an der Kette. Der
Winkel wird durch den Schwalbenschwanz der Rippenplatte gesteckt und
klemmt sich durch den einseitigen Zug fest. |
Leider war die reine Klemmbefestigung nicht 100%
zuverlässig, bei stärkeren Erschütterungen löste
sich gelegentlich eine Schwelle.
Also haben wir "nachgerüstet" und 3 Muttern auf jeden
Winkel geschweisst. Dort einen Federstecker durchstecken, und nichts
kann mehr abrutschen. |
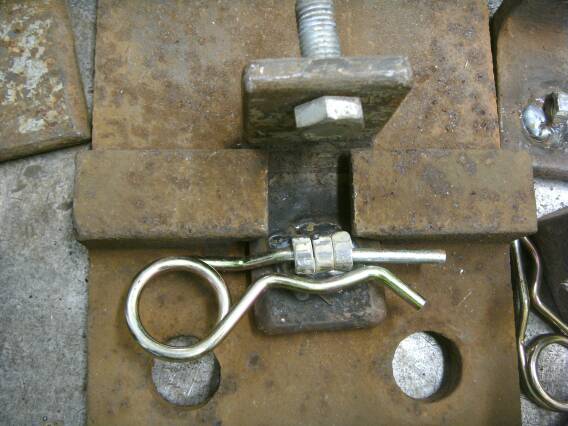 |
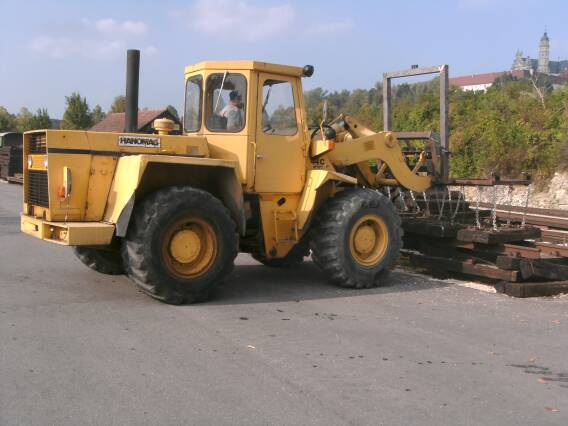 |
Langsam anheben..... |
... und zehn Schwellen hängen am Rahmen, ohne daß
man sie in die Hand nehmen mußte |
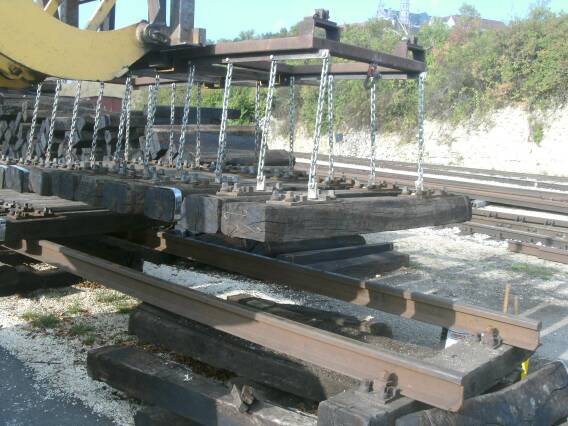 |
vorherige Seite
Copyright © 2009 Gerald Stempel,
Gerald.Stempel@t-online.de
[ Letzte Aktualisierung 03.11.2009 Gerald Stempel ]